The role of DoE in the development of medical devices is extremely important. It is an essential strategy for optimizing the design, manufacturing, and performance of these devices.
It is a systematic approach used to determine the relationship between factors affecting a process and the output of that process. By using the design of experiments strategy, medical device manufacturers and researchers can optimize production, enhance product quality, reduce variability, and meet regulatory standards.
DoE accelerates product development, reduces costs, and enhances the safety, reliability, and performance of medical devices.
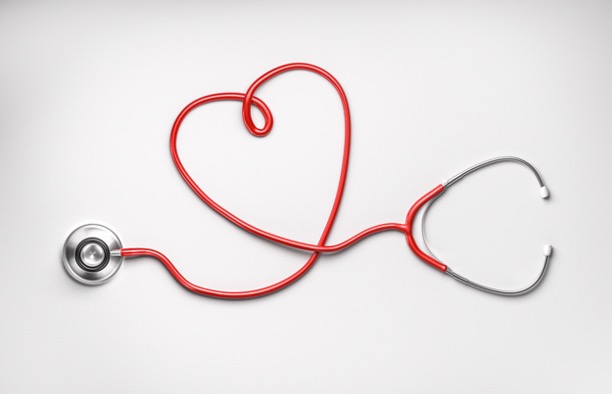
An overview of the role of DoE in medical device development follows:
Optimizing Device Design
- Identifying key influential factors
- Design parameters & performance testing
- Multivariable optimization
Optimizing Manufacturing Processes
- Manufacturing process variables
- Reducing Variability
- Quality Control (QC)
Accelerating Product Development
- Efficient Experimentation
- Simulation & Modeling
Improving Device Performance & Reliability
- Stress Testing
- Reliability Analysis
- Failure Mode Analysis
Optimizing Device Design
- Identifying Key Influential Factors
- During the initial design phase, DoE helps identify and prioritize the factors that most influence device performance.
- Several experimental designs such as screening designs are available to make sure that important factors are not discarded arbitrarily.
- When designing a prosthetic limb, key factors such as material properties, weight distribution, and joint movement angles can be tested to understand their impact on comfort, durability, and functionality.
- Design Parameters & Performance Testing
- DoE helps in setting the most suitable design parameters (such as dimensions, materials, or configurations) to optimize the performance of the device.
- In the development of a drug-eluting stent, DoE could help identify the right coating thickness and drug concentration for optimal therapeutic effect and minimal side effects.
- Multivariable Optimization
- Many medical devices have multiple factors that influence their performance.
- DoE allows manufacturers to study the interactions between different design variables (e.g., temperature, pressure, or material type) and their impact on device performance, leading to more informed decisions about the final design.
Optimizing Manufacturing Processes
- Manufacturing Process Variables
- DoE is used to optimize the manufacturing processes that produce medical devices.
- Process parameters (temperature, pressure, humidity, etc.) in the production of a catheter or an orthopedic implant can be systematically varied and their effects on the final product tested. This helps ensure consistent quality and performance while minimizing defects.
- Reducing Variability
- In the production of medical devices, variability can affect product quality, performance, and safety.
- By applying DoE, manufacturers can identify and control sources of variability, ensuring that each device meets the required standards.
- in the production of a pacemaker, DoE can help identify factors (e.g., component materials, soldering temperature) that may affect its electrical performance and longevity.
- Quality Control (QC)
- DoE allows manufacturers to design experiments that assess the impact of different variables on the quality of the final product, reducing waste and ensuring that devices meet strict regulatory standards.
- By testing different combinations of production parameters, the optimal conditions for manufacturing a consistent and high-quality product can be determined.
Accelerating Product Development
- Efficient Experimentation
- Traditional trial-and-error methods can be time-consuming and resource-intensive.
- DoE allows for more efficient experimentation by testing multiple variables simultaneously in a structured way. This reduces the time needed for development while ensuring that all critical factors are tested.
- Simulation & Modeling
- In addition to physical testing, DoE can be used in simulation and modeling of devices to predict their performance under different conditions.
- Hence, this helps in making informed decisions without needing to conduct exhaustive physical testing, saving both time and cost.
Improving Device Performance & Reliability
- Stress Testing
- DoE can help optimize stress testing by assessing how different device configurations perform under extreme conditions (e.g., high pressure, temperature variations, wear and tear).
- For an implantable device such as a pacemaker, DoE can be used to evaluate how different designs respond to mechanical stress or prolonged electrical activity.
- Reliability Analysis
- Reliability is critical in medical devices, and DoE helps assess and improve the reliability of devices by analyzing various factors that could affect performance over time.
- By testing different combinations of materials, manufacturing methods, and environmental factors, manufacturers can identify designs that are most likely to remain functional over the device’s intended lifespan.
- Failure Mode Analysis
- Through DoE, manufacturers can study potential failure modes in the device by varying conditions such as temperature, pressure, or movement.
- This helps in designing devices that are less likely to fail under real-world conditions, such as a blood glucose meter being used in diverse environmental settings.
The following table provides an overview of the most frequently covered topics. In practice, the exact program is established based on the client’s specific context and identified needs.
Enhancing Regulatory Compliance
- Meeting regulatory standards
- Statistical evidence for approvals
Cost-Effective Development
- Resource optimization
- Minimizing waste
Handling Complex Interactions Between Variables
- Detecting synergies/interaction effects
- Optimizing multivariable systems
Enhancing Post-Market Surveillance & Device Improvement
- Post-Market evaluation
- Continuous improvement
Enhancing Regulatory Compliance
- Meeting Regulatory Standards
- Regulatory bodies such as the FDA have strict requirements for the safety, efficacy, and performance of medical devices.
- DoE helps manufacturers design products that meet these regulatory requirements by systematically testing and optimizing the device’s performance according to guidelines.
- By ensuring that devices are tested under different conditions, DoE provides robust evidence for regulatory submissions.
- Statistical Evidence for Approvals
- DoE helps gather statistical evidence that can be used to prove a medical device’s performance and reliability to regulatory authorities.
- When applying for approval for a new diagnostic tool, DoE can be used to demonstrate the reliability and accuracy of the device in detecting specific medical conditions, reducing the risk of product recalls or approval delays.
Cost-Effective Development
- Resource Optimization
- DoE allows manufacturers to optimize the use of resources in the development and manufacturing processes.
- By testing multiple factors simultaneously and focusing on the most impactful variables, DoE reduces the number of experiments required, which can lower development costs.
- Minimizing Waste
- In medical device manufacturing, waste reduction is crucial for cost-effectiveness and environmental sustainability.
- By optimizing process variables, DoE helps minimize material waste during production, improving overall efficiency.
- In the production of an orthopedic implant, DoE can identify the most efficient manufacturing process that reduces the amount of scrap material.
Handling Complex Interactions Between Variables
- Interaction Effects
- Medical devices often involve complex interactions between various design and process variables. DoE helps in understanding how these interactions affect the device’s performance.
- In the design a drug delivery system, DoE could identify how the combination of drug release rate, material properties, and environmental factors (e.g., body temperature) affect the overall therapeutic effect.
- Optimizing Multivariable Systems
- Some medical devices, such as combination products (e.g., a drug-eluting stent), involve the integration of various components (device and drug) that need to work together.
- DoE can optimize the interplay between these components, ensuring that the system functions optimally and effectively for patients.
Enhancing Post-Market Surveillance & Device Improvement
- Post-Market Evaluation
- After a medical device is launched, DoE can be used to evaluate how changes in manufacturing processes or device design impact device performance or patient outcomes in the real world.
- DoE can help assess how changes in the material of a catheter or surgical instrument impact its longevity, comfort, or complication rates.
- Continuous Improvement
- As medical device technology advances, DoE provides a structured framework for continuous improvement.
- Manufacturers can use DoE to test new materials, device features, or manufacturing processes that enhance performance or reduce costs over time.
Some Applications of DoE in Medical Device Development
- Implants
- In designing an orthopedic implant, DoE is used to identify the optimal materials, surface treatments, and structural design to maximize biocompatibility, durability, and patient comfort.
- Diagnostic Devices
- For diagnostic tools like blood glucose meters, DoE helps optimize the performance of sensors, ensuring they provide accurate readings under different conditions.
- Drug Delivery Systems
- In the development of devices such as insulin pumps or drug-eluting stents, DoE helps optimize the device’s delivery mechanisms and dosage levels to ensure maximum efficacy and safety.
Conclusions
Design of Experiments (DoE) is a powerful statistical methodology in the medical device development process, helping to optimize design, manufacturing, and performance, while ensuring compliance with regulatory standards. By allowing systematic testing of multiple variables and their interactions, DoE accelerates product development, reduces costs, and enhances the safety, reliability, and performance of medical devices.
The use of DoE contributes to better patient outcomes, as devices are designed with optimal functionality and durability in mind.